billet stainless ?
Sheet Steel ?
They are made from tube mild steel that is heat pressed and then cut in half.
Ron makes them from stainless that is pressed to form a collar and then cuts them in half. Same as the original process without the heat press. Very easy to do with the right tooling.
You can also do them in a lathe and spin the tube of stainless and form the lip 
Couldn't resist telling me I'm wrong but like a lot of things you look but you don't see.
So lets look at an exhaust collet, I've worked on 22 of them, grinding the rust off them, polishing them to get a decent finish for the ceramic coating, visually inspecting them for damage and that gives you some insight on how they were made. I didn't consider they were made from tube as the evidence doesn't support that, you've probably handled loads of them but they'll be rusty as a rule and not something worth really looking hard at. Even new ones will have just been fitted without inspecting and I get that, if I hadn't handled and inspected so many recently I'd probably have come to the same conclusion.
So lets examine one, first off they are not circular, they look circular but put 2 together and they don't form a circle unless that circle is elliptical, you're missing the fact they've been cut I hear you say but unless the hacksaw or whatever was used was about 5mm wide they weren't part of a tube to begin with. They are also of different sizes, put a few together and you find they don't match in diameter, fit a pair in an exhaust clamp and you'll see they don't meet, there's a big gap between them. Surely if they were using a tube they'd have got the diameter right, they are engineers aren't they? If I was an engineer tasked with producing these back then I'd have measured the exhaust pipe, roughly about 38mm, now the inside of the exhaust clamp, 44m wide, so I need a piece of tubing 38mm ID and I need to flare that out to 44mm, as Moorey says, make a former and it should be easy. BUT that still leaves you with a 38mm circle and these don't have that.
The evidence supports that these were made of sheet steel, cut to a certain length, folded at 90 degrees and then hydraulically formed into the half circle shape. So what's the evidence? Firstly, study the way the edges have been cut, not been cut with a hacksaw as the state of the edge doesn't have the markings these saws leave, they were hydraulically shear cut, this leaves an bevel on the edge where the metal comes under compression before the shear can start, look closely and you can see this bevel goes around the corner where it's bent, this means it was cut BEFORE the metal was shaped to form the 90 degree fold. If it had been cut after the shape would be totally different. Next bit, if the bend was formed by using a former it would be a gradual shape, look at the ones Ron has made, a lovely slope where the metal has been forced outwards, totally unlike the OE collet, that's a clean bend, almost 90 degrees only distortion is right where it's been bent and that would be normal.
Study this pic of a brand new collet, you can see the shear markings on the edge, you can see them follow the bend, if you look hard you can see the very upper edge of the bend has a small bump on it, clearly excess metal from when it was bent being squeezed out, you wouldn't get that if it had been cut, it would be clean. There would I would also say been no heat involved, cold pressed and that's why there are stress cracks on the edges of the bend, as it's curled into shape by the hydraulic press the metal would have been stretched to almost it's limit and it fractured the edges very slightly as a result, not every collet shows these fractures but enough did to make me notice it when I was dressing the edges down.
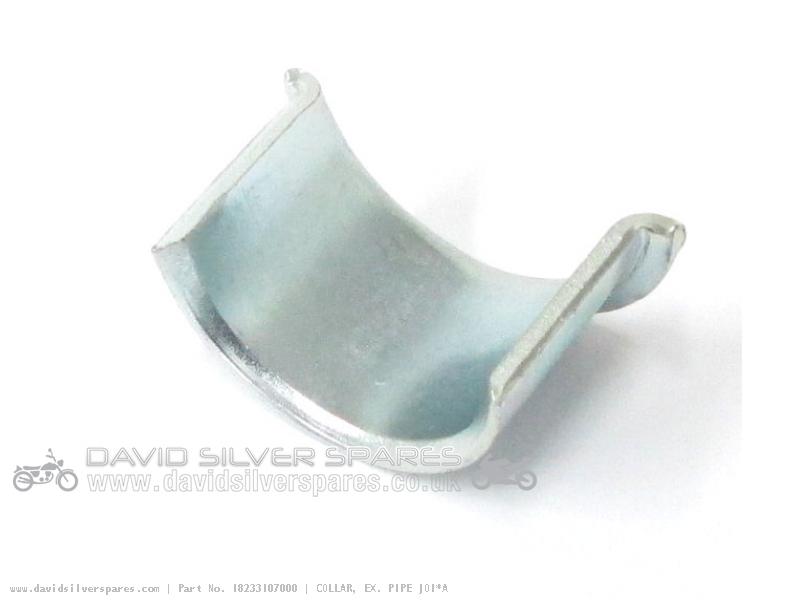
Also look at the bottom edge, it's been radiused where it clamps against the exhaust flange, sure you could radius a tube but why bother, it's a lot easier to do when it's in a sheet, just a simple 30 degree cutter running along the edge.
I'm not an engineer, never studied to be an engineer but I do like to study and imagine how things were made, I do agree however that cutting a tube on a lathe to form the lip would be a great way to produce these but that's lots of waste metal and setting up and lathe time etc and it's a lot easier and cheaper to just cut and fold metal and then hydraulically press them into shape and lets be honest, Honda did things the cheapest way and not always the best way.